
Preferential or prescribed orientation of the fibers leads to the creation of anisotropic materials, which display resistance to certain deformation modes ( O’Connor, 1977 Beter et al., 2020 Chatterjee et al., 2021).
Under uniaxial tension, the same “J-shaped” stress-strain curve seen in aorta and many other biological tissues is also observed. Specifically, the elastomeric matrix provides a robust and deformable base for the material which allows it to withstand many different stresses, while the stiffer fibers act as a reinforcement to prevent excessive deformation under large stress magnitudes. Fiber-elastomer composites, which consist of stiff fibers embedded within a compliant elastomeric matrix, have garnered much attention in the scientific community for their properties which combine the most desirable aspects of both component materials. ( Zhalmuratova et al., 2019) suggested the use of fiber-elastomer composites as material for this compliant tubing. This replicates the function of human aorta, which displays this behavior in vivo and displays a distinct “J-shaped” stress-strain curve when tested under uniaxial tension. The tubing immediately connected to the donor organ in this device is on the centimeter scale and should ideally be compliant enough to act as a shock absorber for the pulsatile fluid flow (which occurs at pressures in the tens of kPa) without being so compliant as to rupture during operation ( Zhalmuratova et al., 2019). One such instance is the ex vivo heart perfusion device (EVHP), a medical device which keeps a donor heart alive ex vivo by connecting it to a tubing system and pumping a blood substitute through it ( White et al., 2013). Larger-scale elastomeric channels with strictly regulated distension behavior must accommodate for different fluid flow properties as well as greatly increased volumetric forces-especially so in hydraulic instances, where the fluid is incompressible and its density may easily be hundreds of times greater than commonly used gases. However, these devices are generally on the scale of tens of micrometers, where the prevailing fluid forces are viscous rather than volumetric. Applications range widely, from drug delivery to agriculture to lab-on-a-chip devices ( Zhang et al., 2020 Zhangzhong et al., 2013 Doh and Cho, 2009). This is generally accomplished by designing a channel with elastomeric walls which contract as pressure increases, regulating the flow rate (or restricting it entirely if pressure is sufficiently high) although more complicated designs have been reported ( Mosadegh et al., 2010). Use of bare elastomers to passively regulate flow in microfluidic channels has been previously reported in literature for many decades ( Chappel, 2020). Components which can passively respond to fluid behavior due to their inherent material properties are specifically valuable, as design of an integrated system to actively monitor and respond to changing fluid flow can be very expensive from both a logistical and financial standpoint. Incorporating custom-designed kirigami relief patterns in the “jackets” expands the potential of the elastomeric tubes.įrom robotics, to industry, to medical devices, development of system components which can accurately respond to and control a flowing fluid has become an incredibly important endeavor. A three-dimensional finite element model predicts the distension of all tested tubes quantitatively across the entire experimental pressure ranges and beyond. In addition, highly asymmetric distension, common to elastomeric tubes due to imperfection in fabrication, is prevented dramatically by the “jacket”. The jacketed tubes initially deform rapidly as pressure increases, but a self-regulation behavior suppresses the tube’s continued distension by strain-stiffening of the “jacket”.
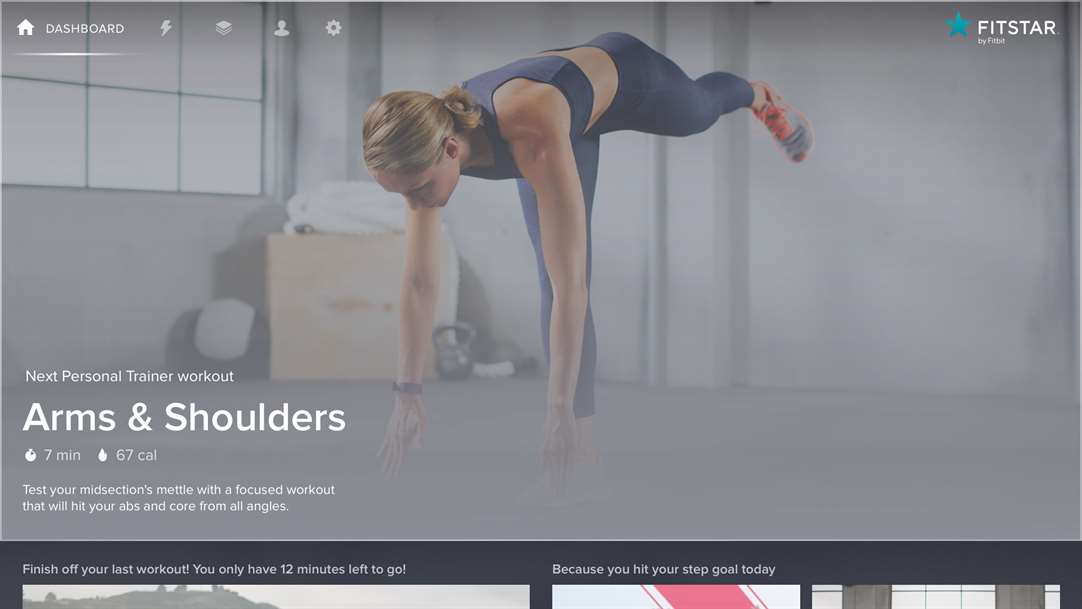
A custom hydraulic pressure testing rig was built to perform experiments.
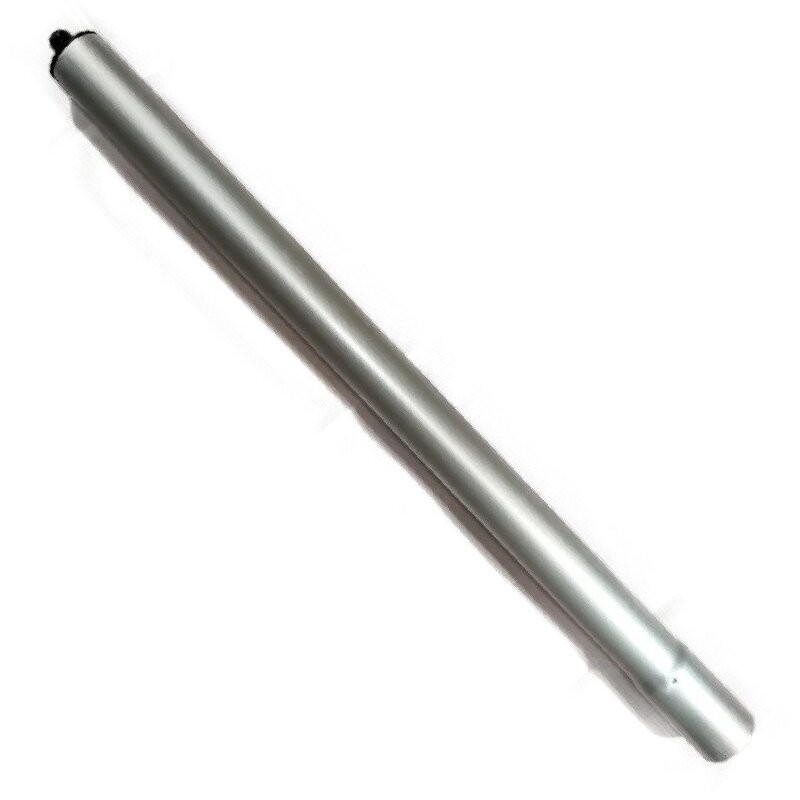
Here, our study shows that a similar design concept can be an effective strategy in realizing passive regulation in the tube’s distension, as well as in preventing aneurysm-like asymmetric rupture of the tube. Compliant elastomer tubing with a fabric “jacket” has been essential in various applications as soft robotic actuators, such as in biomedical exomuscles and massage therapy implements.
